Zodiac
Special Features
Ballistic Recovery Systems (BRS)
The parachute system is designed to protect occupants
in the event of an emergency by lowering the aircraft to the ground after
deployment. Ballistic Recovery Systems (BRS) revolutionized general aviation
safety by providing an alternative measure of safety to occupants.
To deploy the parachute, a person must use
approximately 35 pounds of force on the red handle to set off a magnesium
charge that ignites a solid-fuel rocket. The rocket blows out a hatch where
the BRS is stored. As the rocket deploys, the aircraft will slow as the
embedded BRS harness straps unzip from both sides of the fuselage.
Within seconds, the parachute will unfurl to assist
the aircraft descent. |
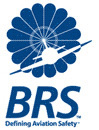
|
Redesigned - the Zodiac CH 650 B:
The original Zodiac was designed by renowned aeronautical
engineer Chris Heintz in the mid-eighties. The design has been a popular
kit-plane since then, marketed and produced in the US by Zenith Aircraft
Company. More than 1,000 Zodiac aircraft are flying throughout the world
today. Over the years, the Zodiac design has evolved as it was first
certified and then manufactured as a ready-to-fly aircraft in Canada, Europe
and South America, as per local regulations, and now in the USA.
The
Zodiac CH 601 XL aircraft was redesigned for the Light Sport Aircraft category in 2004. The
Zodiac CH 650 B is different than the XL. The 650 B incorporates many changes that were made to the 601 series in Europe
and around the world. The 650 B incorporates the best of everything.
The Most noticeable difference is the canopy and rudder. Other changes
includes lowering of the trailing edge of the wings (lowers the nose of the
aircraft for better visibility), control changes (more balanced), tougher
fuselage (good for flying schools), new canopy latching - locking system
(easier to close and open the canopy), and a lot more. The B designation
incorporates all the latest airframe upgrades which includes a tougher
airframe and ailerons balance weights.
Lightening Protection:
Lightning
protection has become a big concern over the years with many new-generation
light aircraft.
"A
growing new class of kit-built composite aircraft also raises some concerns.
Because owner-assembled, kit-built aircraft are considered by the FAA to be
"experimental," they are not subject to lightning protection regulations.
Many kit-built planes are made of fiberglass or graphite-reinforced
composites. At Lightning Technologies' laboratory, we routinely test
protected fiberglass and composite panels with simulated lightning currents.
The results of these tests show that lightning can damage inadequately
protected composites. Pilots of unprotected fiberglass or composite aircraft
should not fly anywhere near a lightning storm or in other types of clouds,
because non-thunderstorm clouds may contain sufficient electric charge to
produce lightning."
When
certifying the Alarus in the early 90's, Zenair consulted with Lightning
Technologies, Inc. to assist with the process of full FAA FAR 23
compliance. Today, the new Zodiac 650 B benefits from past
research and development and incorporates lightning protection technology
and equipment similar to the Alarus aircraft.
For more
details, please visit:
http://www.lightningtech.com/d~ta/faq1.html
|
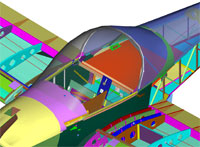
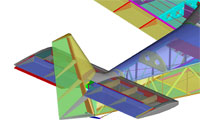
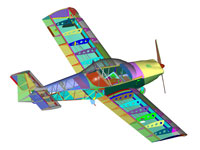
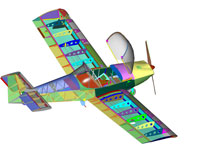
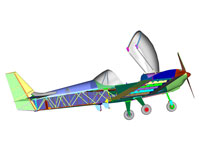 |
|
|
The Engine:
FAA certified under part 33, allowing IFR operations.
Engines are factory new.
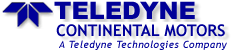 |
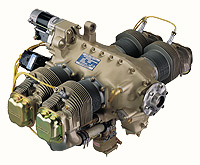 |
ENGINE CERTIFIED UNDER FAA PART 33 |
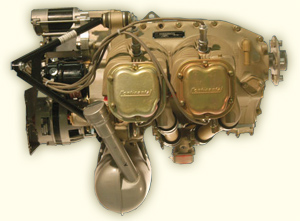 |
Seat Foam |
|
Temper foam, also known as memory foam, was first commercialized during the
mid 60’s as a result of NASA’s AMES Research technology transfer program.
This open-cell variety of flexible polyurethane foam (FPF) was
distinguished by properties allowing it to redistribute the G-Force suffered
by astronauts during take-off and re-entry, and providing commercial pilots
a more comfortable seating surface during long flights. Although
Temper foam production technology has been available for more than 35 years,
commercial products have only recently been made widely available to
consumers.
Temper foam is typified by its slow recovery after compression. When a
weighted object (for example, the human body) is positioned on Temper foam,
the foam progressively conforms to the shape of the object, and after the
weight is removed, the foam slowly reassumes its initial shape. Due to this
gradual recovery, Temper foam also can be described as “slow recovery” foam.
Other
characteristics include Temper foam’s ability to dampen vibration as well as
absorb shock. This latter performance characteristic is confirmed in the
laboratory using ball rebound tests. Ball rebound of less than 20% (compared
to 50% – 60% with other varieties of FPF) supports the description of Temper
polyurethane foam as “dead” or “low-resilience” foam, in that it lacks the
surface “springiness” of other FPF products. In fact, certain Temper foam
products claim to absorb up to 90% of impact.
In
addition to these key advantages, Temper foam also react to body temperature
and ambient temperatures, softening with heat and more easily adjusting to
body contours.
In
the Alarus, Temper type foam is used and is part of the FAA
approved Type Design..
The same foam is available as an option for the Zodiac |
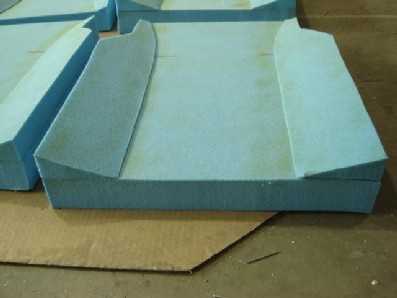
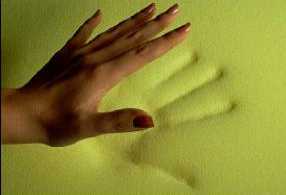 |
|
|
Landing Gear:
The simple
one-piece aluminum
spring gear of the Alarus has been well
tested in the field as many flying schools
throughout the world
are using the aircraft as a primary and
IFR trainer.
The Zodiac gear is similar. Extra tough and simple.
|
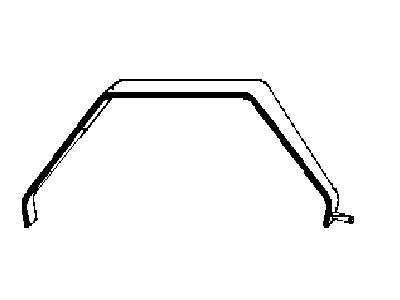
|
Structural Load Testing of the Zodiac: |
|
The ZODIAC design is the product of extensive
research and development, and the result of professional engineering by
Chris Heintz,
a leading designer of light aircraft. The modern design makes use of
advanced technologies, while using proven design concepts and simple systems
for easy assembly and maintenance. A professional design, the ZODIAC
structure has undergone a complete and rigorous flight test and design
stress analysis, as well as load testing of critical components: |
|
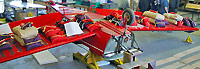
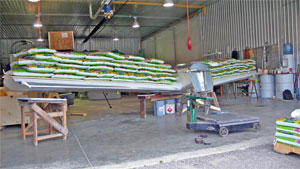
New structural tests again confirms the structural
strength of the 650 B.
Tests were approved and witness by an independent
structural engineer.
|
|
|
Avionics:
The Fast Stack Approach
Harness makes it simple to upgrade as many avionic systems are incorporated
into the Pro-G Wiring System. It's like a plug-and-play system. Each cable
and lead is clearly marked. Instead of having hundreds of individual wires
behind your panel, you have a few. The installation is clean and easy to
maintain.
When a significant
amount of Garmin and other avionics are installed, the Approach Pro-G system is used. |
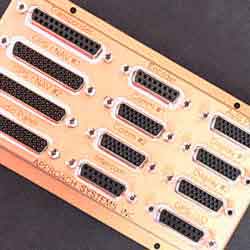
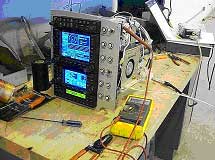 |
.
Transponder-Encoder and pitot static
tests:
In order to meet requirements of FAR 91.411
(...No
person may operate an airplane, or helicopter, in controlled airspace under
IFR unless...Within
the preceding 24 calendar months, each static pressure system, each
altimeter instrument, and each automatic pressure altitude reporting system
has been tested and inspected and found to comply...). Tests are signed off by an FAA certified person before delivery. Log
book entry must be made.
In order to meet requirements of FAR 91.413 (No
persons may use an ATC transponder.....unless, within the preceding 24
calendar months, the ATC transponder has been tested and inspected and found
to comply...). Tests are signed off by an FAA certified
person before delivery. Log book entry must be made. |
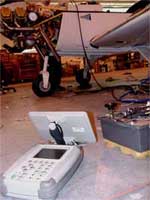

|
ELT:
ELT's are tested and inspected in compliance with FAR 91.207. ELT can be
turned ON at the panel.
|
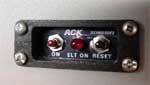 |
|
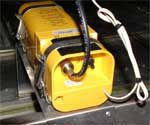 |
|
|
|
|
Aircraft Inspection & Maintenance:
Due to the wide range of available avionics, the top part of the instrument
panel can be easily removed for inspection and maintenance. Rear fuselage
can be accessed through a bottom inspection panel about 2x2 feet big or by
moving the seat backs forward. Other inspection panels are located under the
wings for aileron system and fuel inspection. |
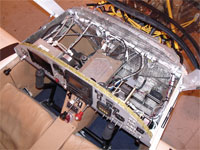 |
|
|
Aircraft Ground Handling:
Nose wheel area is designed so that standard type aviation systems can be
used to move the aircraft.
|
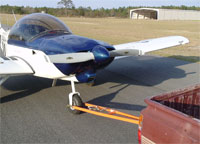
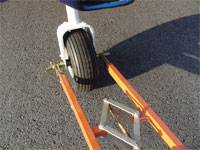
|
|
|
Aircraft Ground Power Plug:
Located behind the wing, away from the propeller. |
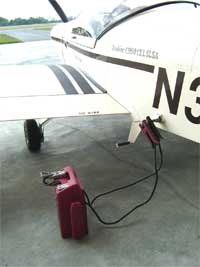 |
|
|
|